Chinese medicine formula particles Screening Solution
The production of traditional Chinese medicine formula granules is based on the decoction requirements of traditional Chinese medicine decoctions, and production process regulation
The production of traditional Chinese medicine formula granules is based on the decoction requirements of traditional Chinese medicine decoctions, and production process regulations are formulated according to different varieties. The basic process route is: selection of traditional Chinese medicine raw materials, processing, extraction, concentration, drying, fine powder screening, granulation, finished particle screening, and packaging.
Traditional Chinese medicine granules are generally made by boiling and drying or granulation mechanisms. During the granulation process, there may be inconsistencies between fine powder and granulation size, waste of labor costs, loss of particles on the ground, direct loss of profits for enterprises, consumer complaints, etc., which are headaches for enterprises. To solve the problems encountered by customers, Gaofu provides one-stop solutions for you.
Screening of raw materials for traditional Chinese medicine
All raw materials used in the production of formula granules are of high quality, and the selection of Chinese medicine raw materials is crucial. Chinese medicine raw materials are purified and sorted through a linear sieve to remove impurities and ensure their quality; Recommended equipment SZF-A linear sieve!
Fine powder screening
After drying, the fine powder is sieved through an 80 mesh sieve to remove some clumps or large particles that may have been added during drying. After sieving, it is sent to the material bin for granulation.
Preferable after granulation
After granulation, a 16 mesh screen is installed on the upper layer, and 30 and 40 mesh screens are installed on the lower layer (depending on the manufacturer's requirements). The upper and lower screens are then fed into the granulation machine through a vacuum feeder for granulation, and the intermediate qualified products are sent to the material bin for packaging. Recommended equipment GFZX pellet sieve!
Introduction of GFZX granule pill sieve
Design for the brittle and easily broken finished particles, light powder density, and poor flowability: the upper, middle, and lower layers of the sieve box are made at different inclination angles; Remove false lumps from the upper layer to reduce repetitive processes; Intermediate finished materials roll forward at a moderate speed, ensuring both production and no breakage. Bottom fine powder, quickly discharged for granulation again without waste.
In response to the pharmaceutical industry's requirements for equipment cleanliness and frequent disassembly, cleaning, and disinfection, we have made humanized improvements to both devices, which are more conducive to workers' operation. In addition, the equipment can be equipped with feeding bins and dust removal devices to improve work efficiency and reduce environmental risks.
1. The dust-free feeding station solves the problem of powder flying during manual material transfer, causing direct waste, and the dust environment directly affecting the health of workers. One device solves two major problems.
2. Particle specific linear sieve: designed for the characteristics of particles such as false agglomeration, brittle and easily broken finished particles, light powder density, poor flowability, etc.: the upper, middle, and lower layers of the sieve box are made at different inclination angles; The adjusted dual amplitude dual motor is attached to the long vibrating plate to transfer the vibration force, allowing the material to be controlled in a single layer on the screen surface (1. For the upper layer with false clumps, the high throw jumps and moves in a straight line to clear the net and hit the jumping ball, solving the problem of false clumps and reducing repetitive processes. 2. For the middle layer of finished materials, roll forward without throwing or jumping, at a moderate speed, ensuring both production and crushing. 3. For the bottom layer of fine powder, with large inclination angles, steep slopes, and short distances, it is quickly discharged for granulation again without waste).
3. Cleaning type dust collector: Automatic negative pressure vacuum mop, replacing traditional manual cleaning, automatically filters and collects the falling materials again, and solves the dust generated during screening vibration, achieving no dust, no waste, and consistent material particles throughout the entire process.
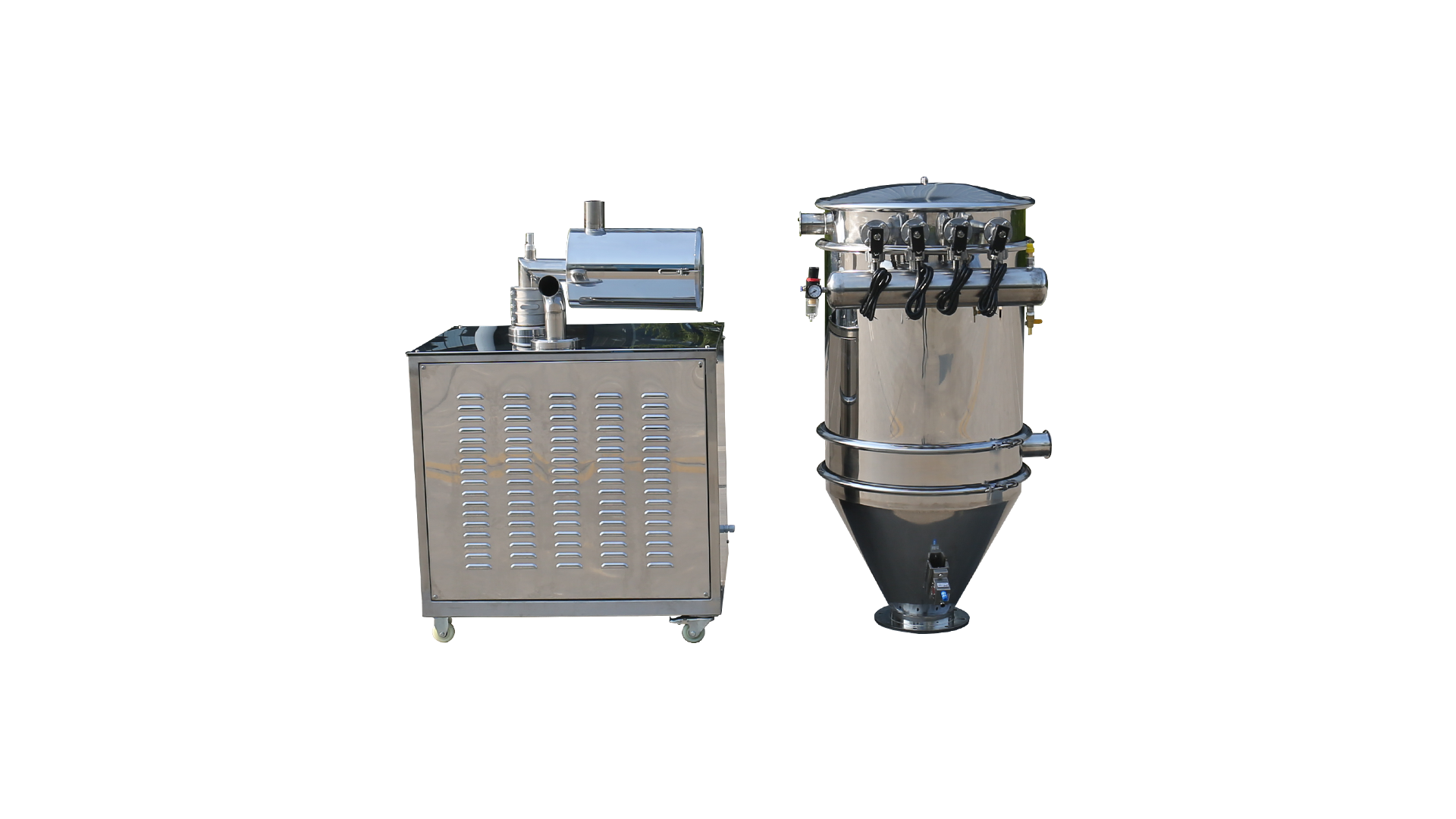
Vacuum feeder
The GFZK vacuum feeder uses a vacuum pump to extract air, keeping the inlet of the suction nozzle an...
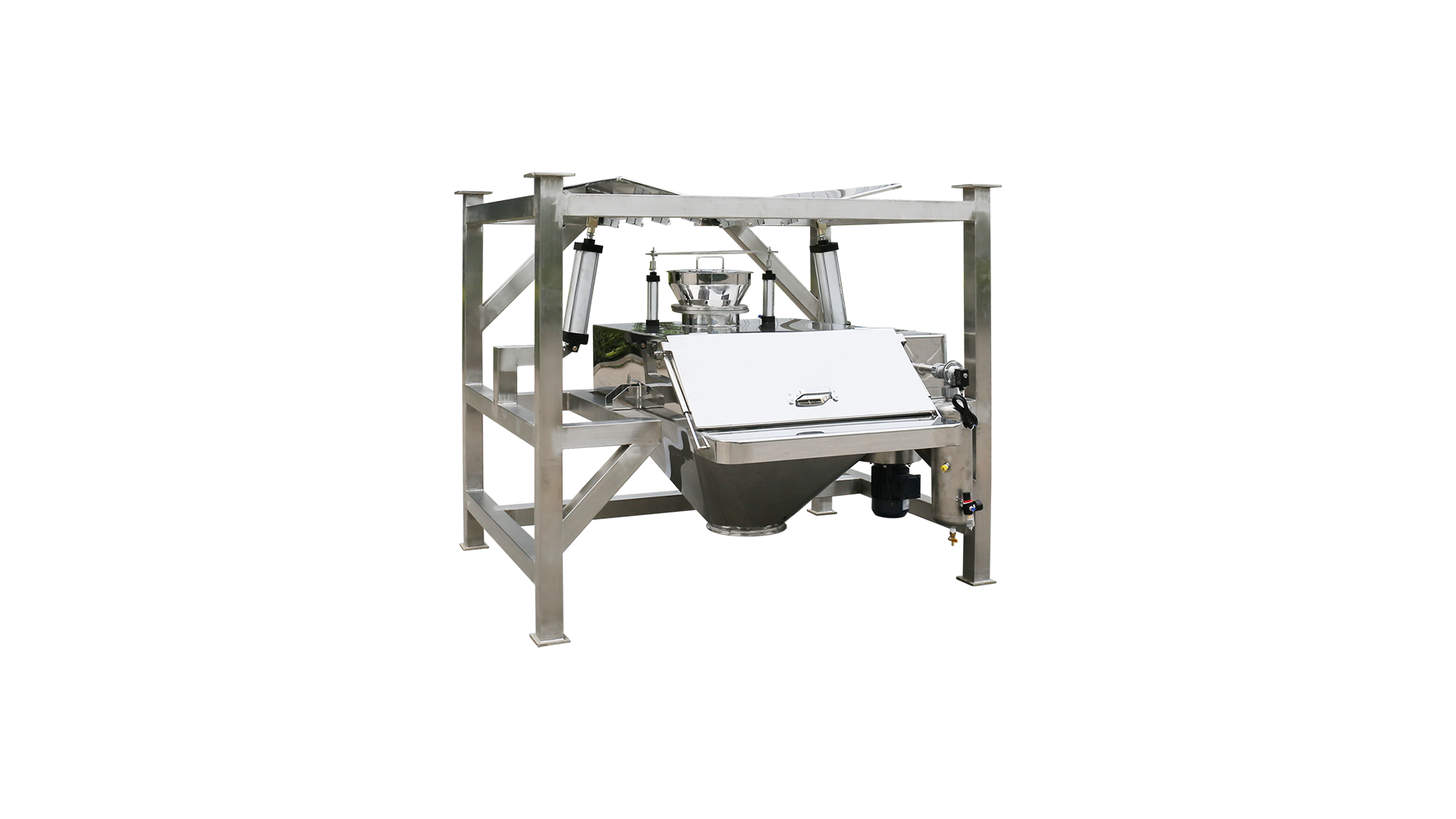
Ton bag feeding station
The ton bag feeding machine lifts the ton bag packaging material to the feeding port. After manually...

Dust free feeding station
Product Introduction:When the small bag material needs to be unpacked and poured into the next proce...