Ceramic powder screening solution
Ceramic powder is called "ceramic powder". The so-called ceramic powder refers to the powdery substance obtained by thoroughly mixing and uniformly calcining (also known
Ceramic powder is called "ceramic powder". The so-called ceramic powder refers to the powdery substance obtained by thoroughly mixing and uniformly calcining (also known as pre firing, pre synthesis) all raw materials during the preparation of ceramics. The chemical reactions between ceramic raw materials do not occur in a molten state, but rather through diffusion between atoms (or ions) at temperatures lower than the melting point, known as solid-state reactions. Therefore, ceramic powders obtained through calcination (pre synthesis) are already pure crystalline substances.
Ceramic powder production process
Raw materials - crushing - ball milling and fine crushing - screening - iron removal - injection molding
Purpose of ceramic powder screening
Screening is the use of a sieve surface with a certain size of aperture or gap to classify materials. After passing through the sieve surface, the powder is classified into two parts: the upper sieve material and the lower sieve material.
Requirement analysis
The first question to consider is what are the requirements for powder size in different industries?
a. The particle size range in the civil engineering and water conservancy industries is ≥ 1cm;
b. The size range of metallurgy, gunpowder, and food industries is 1cm~40um;
c. The size range of the special ceramic powder industry is 40um~50nm;
2. How much traffic is there?
Traffic refers to the processing capacity, which is the amount of screening that a device can complete within an hour. This needs to be calculated based on the size of the material processing capacity. If the processing capacity requires a production capacity greater than 10 tons, a linear screen is definitely recommended. If the production capacity is small, a rotary vibrating screen can meet the requirements.
3. Based on material analysis and screening situation:
There are two types of sieving methods: dry and wet. When measuring particle size distribution, dry sieving is generally used; Wet method can prevent very fine particles from adhering to the sieve holes and blocking them. If the sample contains a lot of water, especially for materials with fine particles, if it is allowed to mix with water and the particles have strong cohesiveness, wet method should be used. In addition, wet screening is not affected by material temperature and atmospheric humidity, and can also change operating conditions, with higher accuracy than dry screening. Therefore, both wet and dry methods are listed as national standard methods for determining the fineness of cement and raw materials.
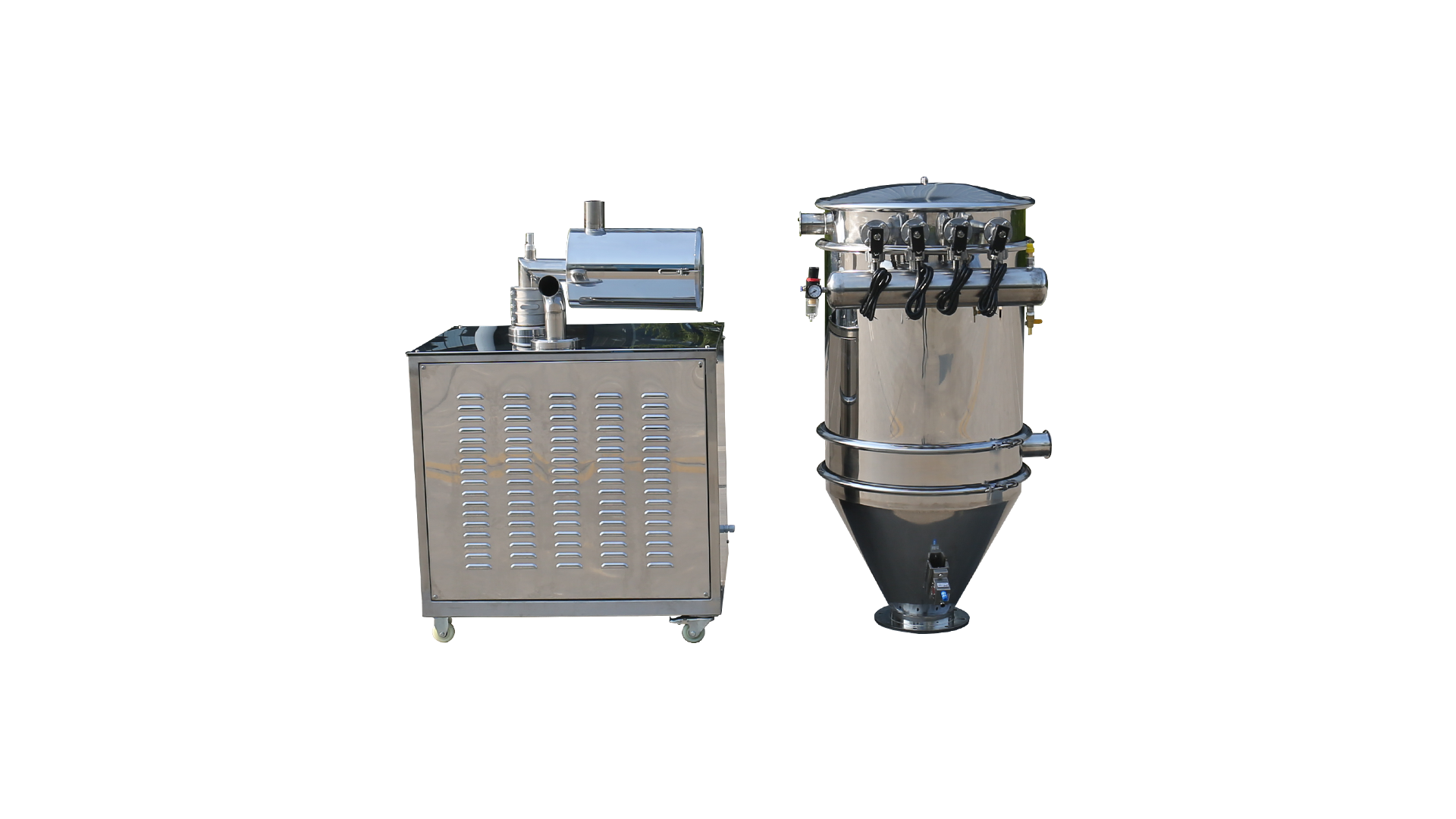
Vacuum feeder
The GFZK vacuum feeder uses a vacuum pump to extract air, keeping the inlet of the suction nozzle an...
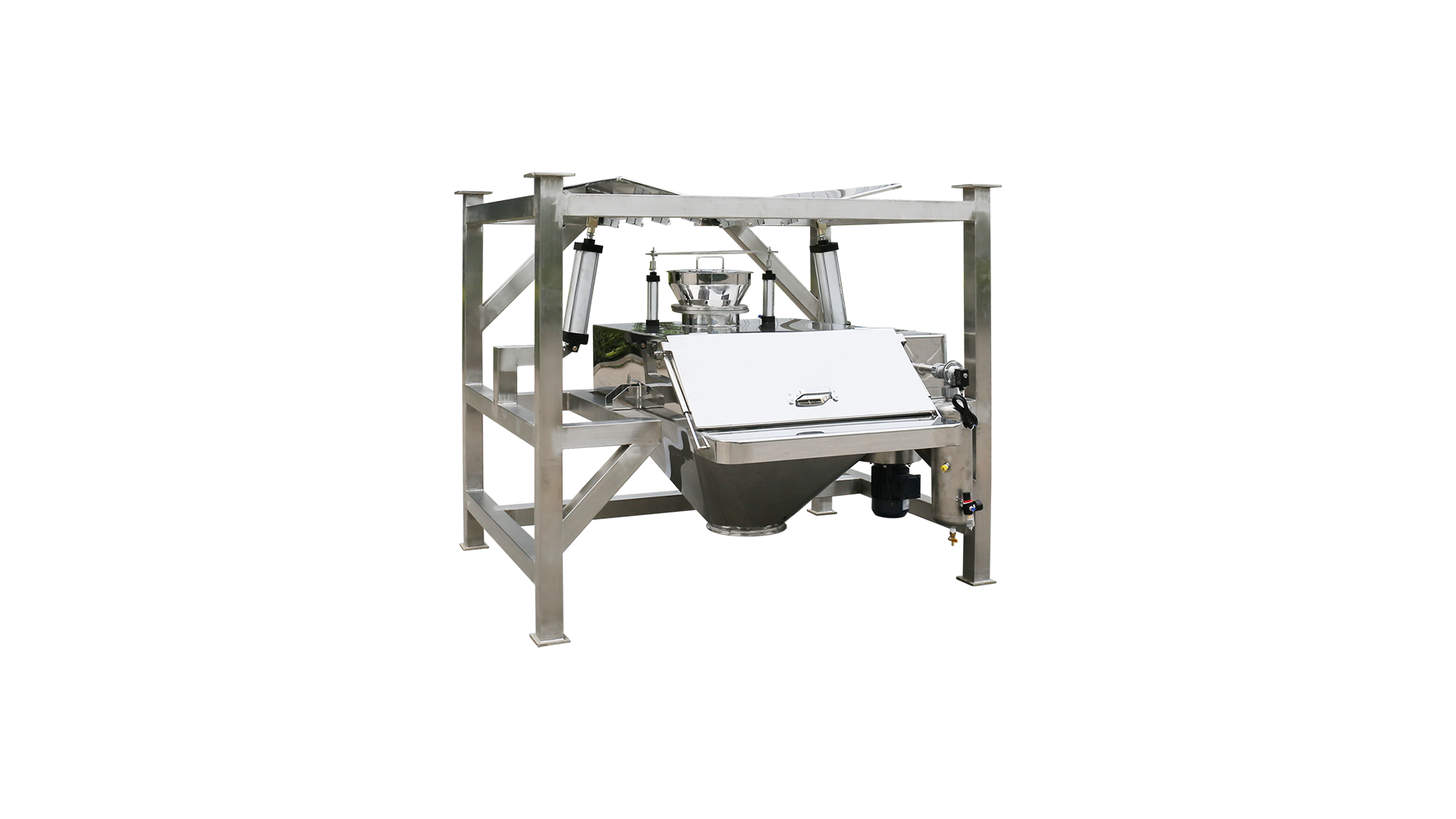
Ton bag feeding station
The ton bag feeding machine lifts the ton bag packaging material to the feeding port. After manually...

Dust free feeding station
Product Introduction:When the small bag material needs to be unpacked and poured into the next proce...